Ever wondered how these components are rigorously tested to ensure they meet the highest standards of safety and performance? Here are some interesting facts you should know.
Importance of Rigorous Testing
When you board a plane, you trust that every component, from the smallest sensor to the most powerful engine, has undergone rigorous testing. This isn't just a formality - it's a critical step in the aerospace industry. Consistent aerospace testing ensures that components can withstand extreme conditions, from the frigid temperatures at high altitudes to the intense vibrations during takeoff and landing. Aerospace engineers know that the reliability of every component is non-negotiable, and testing is the linchpin in achieving this reliability.
Non-Destructive Testing Techniques
To assess the structural integrity of aerospace components without causing damage, non-destructive testing techniques are employed. These methods, including ultrasonic testing and magnetic particle inspection, enable engineers to identify defects or irregularities in materials without compromising their integrity.
Non-destructive testing is particularly crucial for critical components like aircraft wings and landing gear. By employing these advanced techniques, aerospace engineers can catch potential issues early in the manufacturing process, preventing catastrophic failures in real-world scenarios
Simulating Extreme Conditions
Aerospace components must perform flawlessly in the harshest environments imaginable. Testing facilities use cutting-edge technology to simulate extreme conditions, subjecting components to temperature extremes, high pressures, and vibrations. This process, known as environmental testing, allows engineers to identify weaknesses and vulnerabilities, ensuring that the components will endure the challenges of real-world flight.
Altitude Simulation
Testing facilities utilize vacuum chambers to simulate the low air pressure found at high altitudes, ensuring that aerospace components can operate seamlessly in the thin air of the stratosphere. This altitude simulation is crucial for assessing the performance of systems such as engines, sensors, and avionics, providing engineers with insights into how these components function under low-pressure conditions.
Digital Simulation and Modeling
In the digital age, aerospace testing has evolved beyond physical experiments. Advanced computer simulations and modeling now play a pivotal role in testing and refining aerospace components. Computational fluid dynamics, finite element analysis, and other digital tools allow engineers to simulate the performance of components under various conditions.
This not only expedites the testing process but also provides a deeper understanding of how components will behave in different scenarios. Digital simulation is a powerful complement to traditional testing methods, enhancing efficiency and precision in the development of aerospace technology.
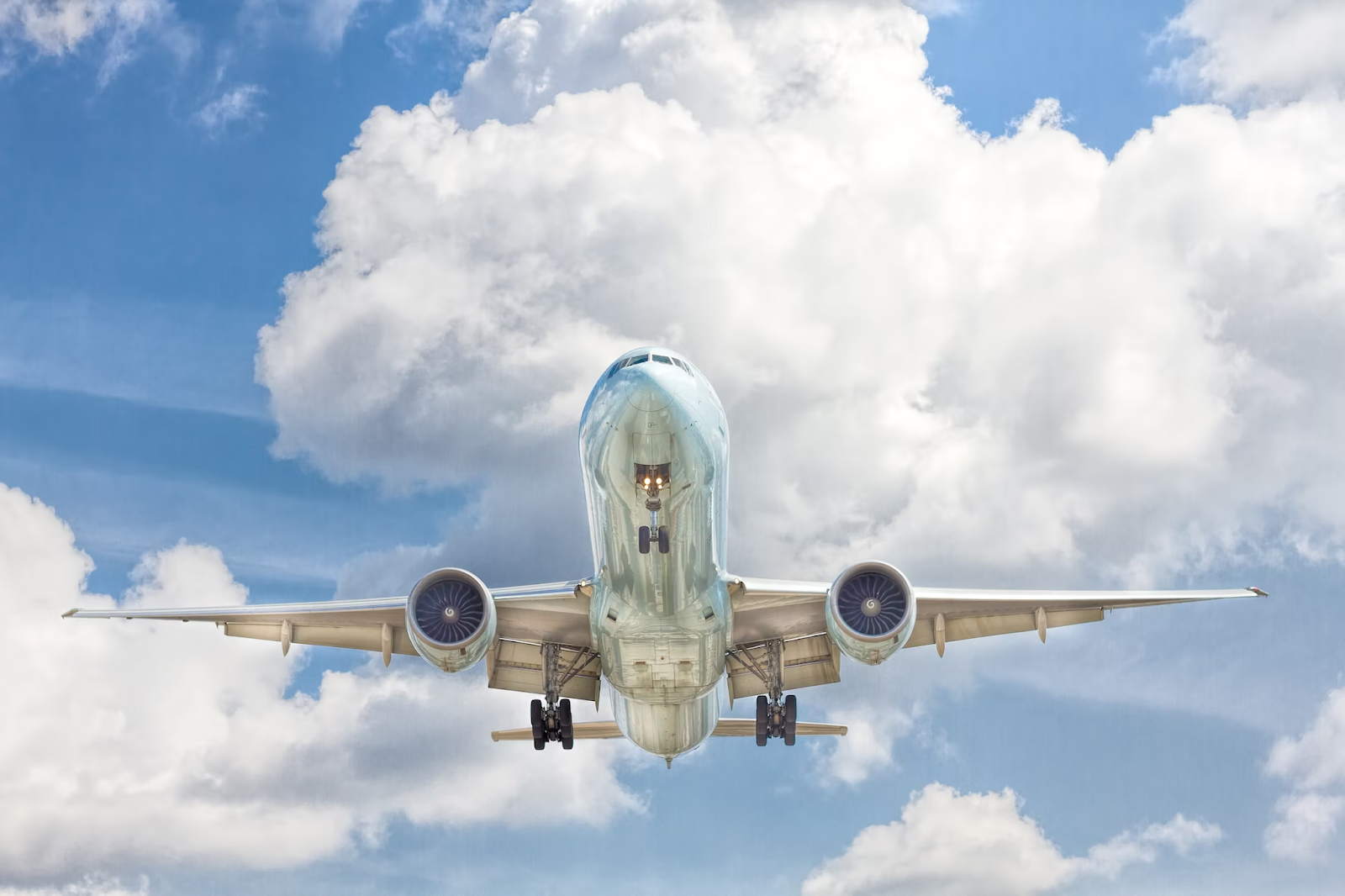
As you settle into your seat on your next flight, take a moment to appreciate the intricate web of testing that ensures the safety and reliability of every aerospace component. The aerospace industry's commitment to rigorous testing is a testament to its dedication to innovation and, above all, your safety.
From environmental simulations to non-destructive testing techniques and digital modeling, every facet of aerospace component testing contributes to the soaring success of modern aviation. It's not just about reaching new heights - it's about doing so with unwavering confidence in the technology that propels us forward.